Process regulator terms
Accessories: installed in actuators to add actuator function, and make it become a complete operating unit device. Examples: including locator, gas pressure regulator, solenoid valve and limit switches.
Actuators: providing force or movement to open or close the valve pneumatic, hydraulic or electric device.
Actuator components: includes all related accessories and makes it into a complete operational units actuators.
Empty processes: provide a dead area general nouns. The dead zone is when a device input changes direction, caused due to device temporary interruption between input and output. A mechanical connected relaxation or loose is empty range typical example.
(valve) circulation ability: under prescribed conditions through one valve flow.
Closed loop (control loop) : a process components mutual connection mode: relevant process variable information is continuously feedback to controller set point, continuously and automatically correcting process variables.
Controller: through using certain predetermined operations to adjust control variables automatic operation device. Controller input accept about process variables state information, and then provides a corresponding output signal to a terminal control component.
Control scope: the control valve can maintain the actual valve gain in the valve stroke scope between standard 0.5 and 2.0.
Regulator components: including usually all the parts mounted on a valve: body assemblies, actuators, locator, pressure regulator, converter, limit switches etc.
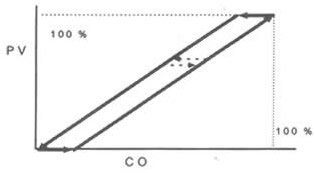
Diagram 1 process dead zone
Dead zone: input signal changes direction but not cause the output signal observed changes, input signals changeable range. Dead zone is used to describe applicable to any device universal phenomenon nouns. To valve components, controller output (C0) is valve component input, while process variables (PV) is the output, as shown in figure 1. When using the term "dead zone", it is necessary to distinguish the input and output, and ensure measuring dead area any measurement in full load test conditions. Dead zone typically expressed as percentage input range.
Diagram 1 process dead zone
Delay time: from a small step input (usually 0.25% --5%) on, system no response detected time length (Td) o, it from step input time to begin measuring, until tested system to produce the first detected response time so far. Delay time can be used for valve components or whole process.
Disc: with linear or rotatry movement, is used to regulate the flow trim components, can also refer to valve core or throttle components.
Terminal control components: the execution decided by controller output control strategy device. Terminal control components can be a shock absorbers, a variable speed driven pump or a on-off type switching device, but in process control industry, the most common terminal control elements are regulator components. Regulator adjusts flowing fluid, such as gas, steam, water or chemical mixture to compensate for a disturbance and allows controlled process variables as much as possible to be near the required set point.
Gain: the general term, can be used in many cases. In its most common sense, gain is a given system or device output change value relative to input change volume ratio that caused the output change volume. Gain has two kinds: static gain and dynamic gain. Static gain is gain relationship between input and output, is when systems and devices in a stable state, input can cause output change degree index. Sensitivity sometimes used to indicate the static gain. Dynamic gain is when the system is in motion or flow condition, the relationship between input and output. Dynamic gain is input changes frequency or rate function.
Lag: in a calibration cycle, relative to any single input value output value of the maximum difference, not including due to dead zone caused error

flow characteristic
Inherent characteristics (flow characteristic) : when through valve pressure drop at constant, with throttle components (disc) from closed position moves to the rated travel process, the relationship between flow coefficient and intercepting components (disc) travel. Typically, these properties can be drawn in the graph, the horizontal axis in percentage terms, and vertical axis trip with percentage flow (or Cv value). Due to valve flow is the valve stroke and the pressure drop through the valve functions, and at a constant pressure lowered for flow
characteristics testing to provide a more valve characteristic type of system method. Using this method measured typical valve characteristic are linear, equal percentage and quick opening (figure 2)
Equal percentage properties: an intrinsic flow feature: rated trip increments will ideally produce flow coefficient (Cv) percentage change (figure 2).
Linear characteristics: a kind of intrinsic flow feature, can use a line in the flow coefficient (Cv value) relative to the rated rectangular diagram trip expressed. Therefore, travel increments provide flow coefficient (Cv) increments.
diagram 2
Quick opening characteristics: the intrinsic flow feature: a small trip in throttle components can gain a big flow coefficient (figure 2).
Inherent valve gain: under constant pressure drop conditions, through the valves flow change value relative to the valve stroke change the volume ratio. Inherent valve gain is the valve structure inherent function. It is equal to the inherent characteristic curve at travel any point slope, but also is the valve stroke functions.
Installation characteristics: when the pressure drop through the valve infulenced by changing process condition, with throttle components (disc) from closed position moves to the rated travel process, the relationship between flow coefficient and intercepting components (disc) travel..
Install valve gain: under the practical process conditions, through the valve flow change value relative to the valve stroke changed volume ratio. Install valve gain is when the valve is mounted in a particular system, and pressure drop is allowed according to the general system of instruction and natural change generated when the valve gain relationship. Install valve gain is equal to install the characteristic curves of slope, also is the valve stroke functions.
I/P: abbreviation of current – air pressure (old UP). Typically used in the input converter module.
Linearity: with two variables related curve and linear close degree o (linearity also refers to the same line in the role of up and down two direction. So, above defined dead zone typically considered as nonlinearity o)
Loop gain: all circuit element is considered as the combination gain in series loop. Sometimes refers to the open-loop gain, sometimes must clearly state refers to the static loop gain or dynamic loop gain.
Open loop circuit: a situation: process control elements connection is interrupted, so, no longer process variable information feedback controller set point, so the process variable correct is not processed. This kind of situation is typically through the controller settings to realize in manual operation state.
Packing: a part of valve components, used for preventing disc or stem leakage.
Locator: a position controller (servo), it's mechanical connected to terminal control components or the actuator moving parts, automatic adjustment to the actuator output, in order to maintain a needed valve position that proportional with the input signal.
Process: control circuit all combinations components in addition to controller. Process typically include regulator components, controlled pressure vessels or heat exchangers, and sensors, pumps and transmitter.
Process gain: controlled process variable changes for the corresponding amount controller outputs change volume ratio. Process deviation degree: how about process is closely controlled in set point around an exact statistics measurement. Process deviation degree typically in percentage defined as (26 / m), in formula m is measured by the process variable set point or average, is process variable standard variance.
Amplifiers: a device whose function is similar to power amplifier. It accepts electric, pneumatic or mechanical input signal, and supply large flow air or hydraulic fluid output actuators. Amplifier can be the locator's an internal components or a single valve accessories.
Resolution: when the input don't change the direction, it is used to produce detected output changes required minimum possible input changes. Resolution typically expressed as percentage input range.
Response time: usually consists of a including delay time and time constant parameters for measurements. (see T63, delay time and time constant). When used for regulator, it includes the entire valve components.
Second order: a term refers to a dynamic relationship between device input and output. One second order systems or devices have two energy storage device. They can in their own back and forth between dynamic and potential energy transmission, thus introducing the oscillation behavior or overshoot possibility
Sensor: a measured process variable's value and provide a corresponding output signals to the transmitter devices. Sensors can be integrating part of transmitte, also can be a single element.
Setting point: a reference value, on behalf of needed and controlled process variable value.
Valve axis twisting: one kind of phenomenon, it refers to the valve spindle end reverse and another end not reverse. This phenomenon is typically occur in actuators by a root relatively longer valve shaft link into valve throttle components rotary valve. When the valve sealing friction to keep one end of the valve spindle remain in a certain position, actuators end valve axis rotation was absorbed by torsion valve spindle, until actuator input to deliver enough force to overcome this friction.
(valve) diameter calculation: through the designed system method, to ensure valve in a series of process conditions with right circulation ability.
T63: equipment response time measurement. It is through a small step input (usually - 5%) act on system to measure oTc, measuring from the time when step input began, until the system output reached 63% final steadystate value time so far. It is the system delay time (Td) and the system time constants (t) combination values. (see "lag time" and "time constant").
Time constant: a time parameter commonly used for first-order element. It is from system produced first step input relative small phase step input(usually 0.25% - 5%) can detect response to system output reached 63% final steadystate value measured time interval. When used for an open loop processes, time constant usually expressed as To used in closed loop system, time constant usually expressed as a pill.
Transmitter: a variable's value measurement process and provide a corresponding output signals to the controller by comparison with set point device.
Trip: throttle components from the closed position to an intermediate or nominal full open position movement.
Trip indicator: a pointer and stick, used to from external said throttle components position, typically using the percentage of travel or rotating angle as unit.
Trim: adjust controlled fluid valve internal components. Fluid supercharger: an independent amplifiers are usually called fluid supercharger or simply supercharger, because it increases force port or enlarge supply actuator compressed air volume. (see "amplifier ')
Actuator thrust: actuators provide net force that could be used to make actual valve core localization.
Angle valves: one type of valve structure, one of its port and the stem or actuators in a straight line, another port is a vertical angle with stem.
Bellows seal type bonnet: use bellows to prevent around throttle components link rod leakage bonnet.
Bonnet: valves contain stuffing box and stem seal and can guide stem part. It provides the main valve opening pore, for installing internal parts, can also be an inalienable part of the body. It puts actuators connected to the body. Typical bonnet and body is bolted connection, thread screwed, welding connection, with pressure seal, or integrated not separated. (this term generally refers to the bonnet and contains packing parts. The more add accurately, this group of spare parts should be called bonnet components.
Bonnet components: (often called bonnet, more accurately called bonnet components) a component, including stem can be in one movement parts and prevent leakage around stem seal form. It usually provide installing actuators and loaded packing component method.
Bottom flange: a closed body opening pore part that relative to bonnet opening pore.
The cage: trim part, inclusive throttle components and regulations provide seat close flow characteristic or surface. It also supply stability, guiding, balance and neutral, but also help other trims parts assembly. The cage wall contains usually decide the characteristics of flow regulator trapping. Various cage form is shown in figure
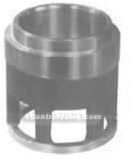
fast open
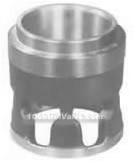
linear
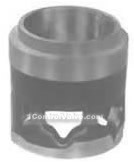
equal percentage
Closure components: the valve moveable parts, it is placed in the fluid path, used to regulate the valve flow. Throttle components oriented surface: throttle component part, it makes throttle components in cage, seat ring, bonnet, bottom flange or above any two parts movement.
Cylinder: piston actuator air chamber, piston in cylinder cover sealing: piston actuators cylinder and support connecting sealing components.
Diaphrag,: an active force transfer to diaphragm support plate and actuator pressure response components.
Film actuators: a fluid actuated device, in which fluid role in a moving parts diaphragm.
Membrane cover: contain two parts shell, used to support the diaphragm and establish one or two pressure chamber.
Diaphragm support plate: the plate that concentric with diaphragm and transfer force to give actuator push rod.
Positive role actuators: a thin film actuator, its push rod with diaphragm pressure increases and stretched out. Elongation type bonnet: a length among bonnet, stuffing box and bonnet flange, used for low or high temperatures condition.
Straight through valve: one type of valve, with linear motion throttle components, with single seat or more seats, its body because the seat area have a spherical inner cavity and different. Straight through valve can be further divided into: two way single-seat valve, two way two seat valve, angle shape, tee, uneven cage orientation and balance cage oriented.
Lower body: contain internal valve parts, a port connection mouth half body shell part. In red-tipped body structure, seat ring is usually pressure between the upper body and lower body. Compensating valve: one type of valve structure, the inlet and outlet pipe connection on different but to each 80 degrees opposite.
Stuffing box (component) : bonnet component part, in order to intercepting around throttle components connected rod leakage. Included in the complete stuffing box following parts some or all combination: packing, gland, packing nut, casing ring, filler spring, packing flange, packing flange studs secures or single head bolts, packing flange nuts, packing ring, packing isolated circle annulus, felt isolated circle, BeIIev川e spring and anti extrusion ring.
Piston: a moveable pressure respond component that can tranfer the force to piston actuator thrust rod.
Piston actuators: a fluid actuated device, in which fluid role in a removable piston to make on actuator push-rod produced movement. Piston actuator can be divided into: dual action type, therefore, in any one direction can produce big driving force; Or is divided into spring return type, therefore lose air, actuators can make valve along the on-demand direction.
Reaction actuators: a thin film actuator, its push rod will return with diaphragm pressure increases. Reaction actuators have a seal bushings installed in the top of the scaffold, in order to prevent the diaphragm pressure along the actuators push-rod bleeder.
Rubber sleeve: a prevent destructive foreign body in the piston actuator seal bushings protective device. Sealing bushings: used to provide a way of avoiding piston actuator cylinder leakage way upper and lower bushing. Synthetic rubber o-ring is used in bushings, seal cylinder, actuators push rod and actuator push-rod lengthen axis.
Seat: throttle components and its surface contact area, it implements seat closure.
Seat load: in the provision of static condition, the net connected force between throttle components and seat. In fact, for a given regulator, actuators choice is need big force to overcome static, stem and dynamic unbalanced force, and leave an allowanceto based for seat load.
Seat ring: a part of body components.
Spring adjustment component: a pipe fitting, usually spin in actuators push-rod or screwed stents inside, in order to adjust the spring compressed volume.
The spring seat: board, maintain spring in place and provide a spring adjust parts contact plane.
Static unbalanced force: in the provision of pressure condition, and fluid in static state, because the fluid pressure acting on throttle components and valve stem produced net force. Stem connecting part: put actuators push-rod link to stem.
Trim: adjust accused fluid valve internal components. In direct body, trims typically include throttle components, seat ring, cage, stem and stem pin. Valve internals and soft seat: with elasticity, plasticity or other easy deformation material trims, used on the throttle components or seat ring, by using minimum actuator force to make tight closure.
The upper body: contain internal valve parts, a port connection port body shell half part. It usually includes a prevent around stem leakage way, and to provide the actuator mounting in fission body method. Valve body: valve main pressure supporting cavity. It also provides pipe connection terminal and fluid circulation channel, and sustaining seating surfaces and valve closure components. The most commonly used body structure are: a) take a seat port and valve core single seat valve; B) with two seat mouth and a valve spool double seat body; C) with an entry and exit two fluid connected two way valve; D) the body with tee fluid connected end, including two connected end can be entrance, and one is outlet (for mixed fluid), or a link end is the entrance, and two are outlet (for decentralized fluid) o term body often used to refer to contain bonnet assemblies and contains trims parts body. The more add accurately, this group of components shall be called body components.
Body assemblies (often known as body or valve, more accurately called body assemblies) : a valve body and bonnet assembly, bottom flange (if used) and trims components assemblies. Trims including closure components, it open and shut or partially blocked one or more seat mouth.
Valve core: One term often used to switch with plug, it refers to the throttle components
Stem: straight trip valve, connect actuators push rod and throttle components parts.
Support: the actuator power unit rigid connected to valve structure.
Actuator lever: connect to rotate the valve shaft's arm. It put actuators push-rod linear motion convert rotating force to locate rotary valve disc or ball. This lever normally is through small clearances spline or other reduce gap and movement loss method connection to rotary valve spindle.
Full ball: rotary regulator fluid control components. It uses a complete ball and the fluid pass through it. Fluid channels and pipe diameter is equal or consistent.
Partial ball: rotary regulator fluid control components. It uses a partial ball with flow through it.
V-shaped notch ball: the most common parts ball regulator type. V-shaped notch ball includes a polished or coating surface part of the ball, it abuts seat ring in the whole trip range for the rotary motion. On the ball V-shaped notch can achieve high adjustable ratio and provide a equal percentage flow characteristics.
Traditional disc: used for the most common various butterfly valve symmetrical fluid control components. In the regulating condition, very high dynamic torque will often combine traditional disc restrictions in 60 degree maximum angle. Dynamic design disc: butterfly valve disc after streamlined contour processing, can reduce big rotary angle increment dynamic torque, thus making it applies to the most necessary to 90 degrees to the disc rotary angle operating conditions.
Eccentric disc: valve structure general term, in this valve structure, valve spindle and disc connection position makes the disc when open along a very small eccentric path movement. This makes the disc in opened as fast as possible to deviation and sealing contact, it reduces friction and wear.
No flanged valves: common rotary regulator type. No flanged valves use long bolt clip between ANSI class flanges (sometimes it is called the wafer body).
Eccentric ball plug: with eccentric spin plug rotating regulator type. Eccentric ball plug will tucked into or depart from the seat, can reduce the friction and wear. This valve is very suitable for scour applications.
Reverse flow: fluid from the disc, ball or ball plug back alve spindle side outflow. Some rotary valve can balanced treat fluid in any direction. Other types of rotary valve may be modified actuator fittings to handle the reverse flow.
Gimbal bearings: often used in the connection between actuators push rod and the actuator lever. Its purpose is to promote actuators linear thrust to rotary force transformation and minimize movement losses. On rotary valve body can be equipped with a standard interchangeable acting direction actuators, usually need to use two gimbal bearings fittings. However, the choice for rotary valve condition and specially designed actuators only need one such bearing, thus reducing the movement losses.
Rotary regulator: a valve type, its fluid throttle components (full ball, partial ball, disc or ball plug) in the fluid path rotation, to adjust the valve flow.
Sealing ring: rotary regulator corresponding to the direct valve seat ring part. Disc or ball relative to the sealing position etermines the circulation trip incremental area and the circulation ability. As the above shows, some sealing structure allows two-way flow.
Valve spindle: rotary regulator corresponding to direct the stem part. Valve axis rotation locates the fluid path disc or ball, so can adjust the valve flow capacity.
Sliding seals: pneumatic cylinder piston actuators below seal, is designed for rotary valve conditions. This seal allows actuators push-rod vertical movement and circular rotation, and won't make next cylinder pressure bleeder.
Standard flow: with independent sealing ring or fluid those rotary flow direction: the fluid through pipe adjacent sealing ring to enter into body and relative to the other side of the outflow. Sometimes called prior flow. (also known as "reverse flow").